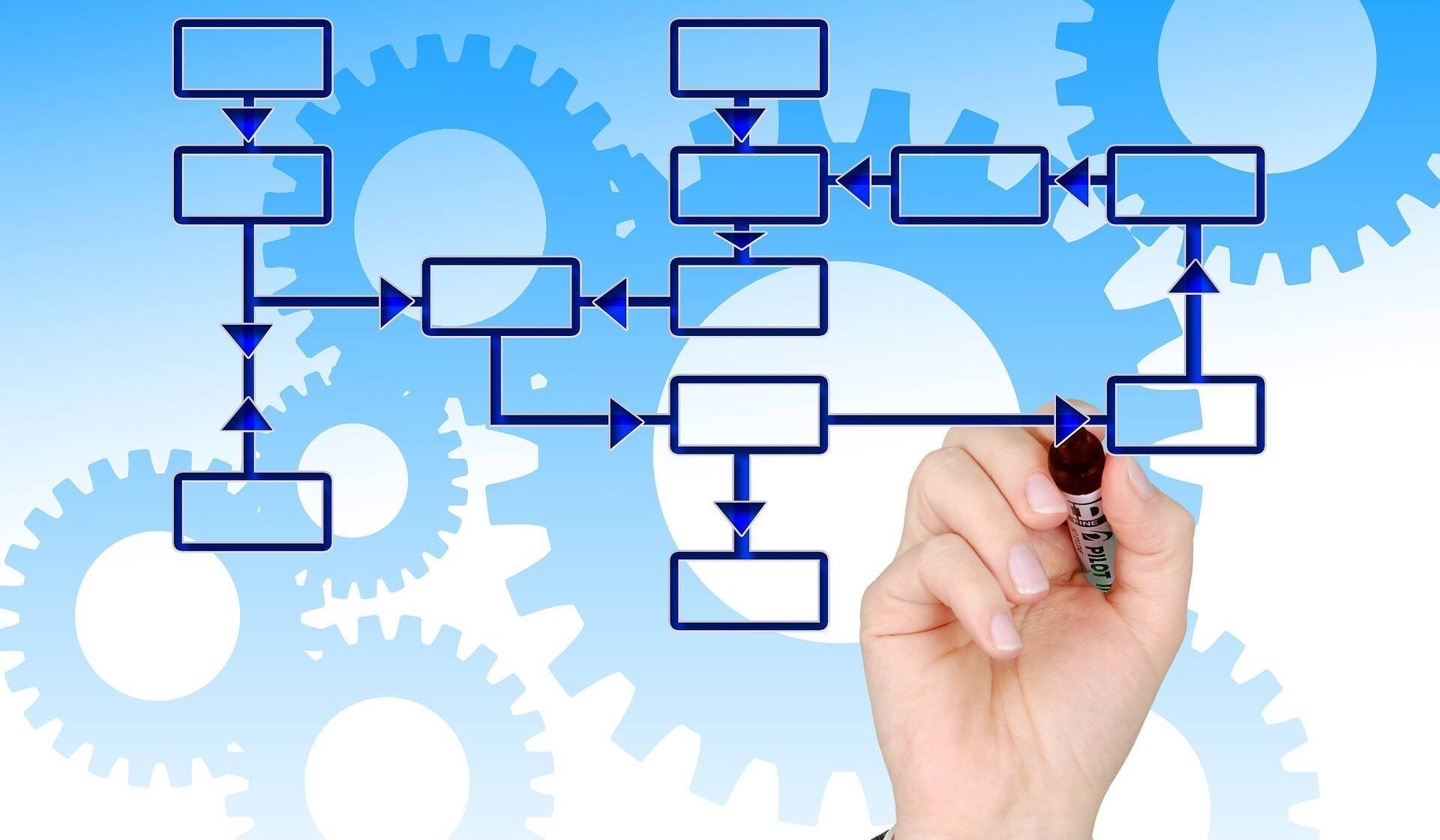
Procesy magazynowe i ich elementy składowe
Magazynowanie, to zespół czynności związanych z przyjmowaniem, przemieszczaniem, składowaniem, ochroną, kontrolą, ewidencją i wydawaniem dóbr materialnych w wyznaczonym do tego miejscu w określonych warunkach.
Z opracowania dowiesz się:
– jakie fazy składają się na proces magazynowy,
– jakie są metody magazynowania, które znajdą zastosowanie w poszczególnych fazach procesu magazynowego,
Magazynowanie wymaga rzeczowych warunków w postaci lokalizacji, wyposażenia do manipulacji, transportu i składowania, personelu i innych środków techniczno – organizacyjnych. Wbrew pozorom współczesny magazyn, szczególnie rozdzielczy, jest strukturą bardzo złożoną i wymaga wieloaspektowego podejścia.
Na proces magazynowy składają się następujące fazy:
- przyjęcie do magazynu,
- złożenie w wyznaczonym miejscu (składowanie),
- kompletacja,
- wydanie z magazynu.
Przyjmowanie towarów, to faza procesu magazynowego. Dostawca przejmuje towary według określonych warunków dostawy. Odbywa się to w wydzielonym miejscu w strefie przyjęć do magazynu i obejmuje następujące zadania:
– sprawdzenie dokumentów dostawy,
– wyładunek dostawy ze środków transportu zewnętrznego,
– przyjmowanie dostawy zgodnie z listem przewozowym oraz sprawdzenie stanu fizycznego przesyłki,
– odbiór ilościowy dostawy na podstawie dokumentacji,
– kontrolę jakościową przeprowadzaną zgodnie z warunkami technicznymi odbioru,
– segregowanie, sortowanie, przepakowywanie i oznakowanie dostawy zgodnie z ustaloną organizacją pracy magazynu,
– formowanie i sprawdzanie jednostek ładunkowych odpowiednio do wymagań technologii składowania,
– zapewnienie ochrony dostawy zareklamowanej,
– zapewnienie ochrony zapasów do czasu przekazania ich do strefy składowej,
– przekazanie dostawy przyjętej do strefy składowej,
– sporządzenie dokumentacji związanej z przyjęciem dostawy.
Charakterystyczny dla tej fazy jest dobór systemu transportowego do przeładunku z odpowiednimi urządzeniami pomocniczymi oraz możliwości sterowania procesem. Znajdą tu zastosowanie:
– ręczny rozładunek w powiązaniu z odpowiednimi urządzeniami pomocniczymi lub środkami transportowymi zależnie od masy ładunku (normy bhp dla prac ręcznych),
– wózki widłowe unoszące i podnośnikowe dla dostaw w postaci jednostek ładunkowych (lub ich formowanie przy rozładunku); zastosowanie wózków zwiększa elastyczność prac rozładunkowych,
– specjalistyczne, automatyczne urządzenia rozładunkowe, których zastosowanie warunkuje dostawy w jednostkach ładunkowych uformowanych na przystosowanych paletach ładunkowych; charakteryzują je wysokie nakłady inwestycyjne, możliwość współpracy z kompatybilnym wyposażeniem na frontach rozładunkowych.
Szybkie, operatywne i efektywne działanie w tej fazie można osiągnąć przez:
- ustalone organizacyjnie czynności przyjmowania,
- stosowanie właściwej technologii rozładunku pojazdów,
- posiadanie odpowiednich procedur postępowania oraz wyposażenia przy kontrolach ilościowej i jakościowej,
- przekazanie przyjętych towarów odpowiednimi środkami transportowymi zgodnie z dyspozycjami do składowania.
Prowadzenie prac przeładunkowych
Do istotnych czynników mających wpływ na technologię przyjmowania towarów do magazynu należą:
- sposób ukształtowania frontu przeładunkowego magazynu,
- postaci przyjmowanych towarów.
Front przeładunkowy magazynu jest to miejsce, w którym następuje proces przeładunkowy towarów (wyładunek lub załadunek) ze środka transportu zewnętrznego na środek transportu magazynowego.
Wyróżniamy dwa podstawowe typy frontów przeładunkowych: bezrampowy i rampowy.
Front bezrampowy, usytuowany na poziomie terenu, ma zastosowanie przy zmechanizowanych procesach przeładunkowych i manipulacji jednostkami ładunkowymi. Wymaga dużej powierzchni stanowisk ładowania dla umożliwienia prowadzenia prac rozładunkowych ze wszystkich stron skrzyni ładunkowej.
Front rampowy, usytuowany na poziomie podłogi burty samochodu umożliwia, poprzez mostek ładunkowy wjazd środków transportowych do wnętrza skrzyni pojazdu, co znacznie przyspiesza dokonywanie przeładunków.
Rampa magazynowa może mieć postacie: czołową (prostą), grzebieniową lub gwiaździstą i umożliwiać rozładunek skrzyni samochodowej zgodnie z potrzebami procesu przeładunkowego. Ze względu na potrzeby prowadzenia prac rozładunkowych środkami transportu oraz różną wysokość skrzyni ładunkowej pojazdu względem rampy wyposaża się je w stałe, uchylne lub przenośne mostki ładunkowe.
Stosowanie bezrampowego lub rampowego rozwiązania frontu przeładunkowego zależy od występujących w rozpatrywanym przypadku od kryteriów technicznych, organizacyjnych i ekonomicznych.
Wprowadzanie w magazynie dostaw według zasady „Just in Time” wiąże się ze wzrostem przepustowości frontów przeładunkowych, co ma wpływ na wzrost liczby bram magazynowych i wydłużanie długości frontu.
Operacje przeładunkowe
W zależności od charakteru wzajemnych relacji pomiędzy postacią przeładowywanych ładunków, urządzeniem przeładunkowym oraz człowiekiem występującym w procesie przeładunkowym wyróżniamy operacje przeładunkowe:
– nie zmechanizowane z ręcznymi pracami przeładunkowymi,
– częściowo zmechanizowane z udziałem urządzeń przeładunkowych oraz ręcznych czynności przeładunkowych,
– zmechanizowane (zautomatyzowane) z mechanicznym przeładunkiem za pomocą urządzeń przeładunkowych.
Prace nie zmechanizowane występują przy ręcznym rozformowywaniu skrzyni ładunkowej pojazdu samochodowego lub kontenera oraz przemieszczaniu ładunku drobnicowego (w opakowaniach transportowych) ręcznie, wózkiem naładownym lub przenośnikiem specjalnym o zmiennej długości na pole odkładcze strefy przyjęć.
Prace częściowo zmechanizowane z udziałem urządzeń przeładunkowych oraz ręcznych czynności przeładunkowych występują przy ręcznym formowaniu jednostek ładunkowych z opakowań transportowych i ręcznym przemieszczaniu ładunku wózkami widłowymi unoszącymi lub podnośnikowymi.
Prace zmechanizowane (zautomatyzowane) z mechanicznym podejmowaniem i przemieszczaniem ładunku występują przy podejmowaniu i przemieszczaniu ładunków w postaci jednostki ładunkowej za pomocą wózków widłowych podnośnikowych, przenośników wałkowych, suwnic specjalnych wyposażonych w uchwyty do podejmowania ładunku (widły lub trzpień).
Usprawnianie procesów przeładunkowych
Przy usprawnianiu procesów przeładunkowych najistotniejsze znaczenie mają ich mechanizacja i operowanie jednostkami ładunkowymi w całym łańcuchu dostaw. W zależności od powiązań gospodarczych i handlowych w łańcuchu dostaw są stosowane specjalizowane pojazdy samochodowe wyposażone w urządzenia umożliwiające zautomatyzowany przeładunek, wymagające wyposażenia zewnętrznego frontów przeładunkowych w takie same urządzenia, np. przenośniki wałkowe wmontowane w nawierzchnie rampy i w podłogę skrzyni pojazdu, na których są ustawiane jednostki ładunkowe. Prostsze urządzenia montowane na pojazdach a mające zastosowanie w rozładunkach to np. żurawiki lub małe urządzenia dźwigowe.
Kryteria doboru środków transportu do prac przeładunkowych i przemieszczania
Ważnym elementem, mającym wpływ na efektywność pracy, jest stosowanie odpowiednich środków transportowych (wózków) oraz ich dobór do konkretnych prac, takich jak:
- przemieszczanie z frontu przeładunkowego na pola odkładcze strefy przyjęć,
- przemieszczanie ze strefy przyjęć do strefy składowej.
Przy doborze środków transportowych należy rozpatrywać jednocześnie następujące warunki:
– odległość przemieszczeń,
– nośność lub udźwig środka transportowego.
Odległość przemieszczeń
Wykorzystanie środków transportu zależy w głównej mierze od ich cech ruchowych i geometrycznych, przy uwzględnieniu specyfiki organizacji pracy w danym magazynie.
Przy rozładunku i przemieszczaniu jednostek ładunkowych stosuje się wózki jezdniowe w zależności od długości dróg transportowych zgodnie z następującymi zasadami:
- Wózki jezdniowe unoszące ręczne do prac rozładunkowych środków transportu zewnętrznego oraz przemieszczeń jednostek ładunkowych na odległość do 30m, wózki jezdniowe unoszące z napędem elektrycznym – od 30 do 80m.
- Wózki jezdniowe podnośnikowe o niskiej wysokości podnoszenia wideł (do ok. 2,5m) na odległość do 80m, z jednoczesnym piętrzeniem jednostek ładunkowych na polu odkładczym strefy przyjęć.
- Wózki jezdniowe podnośnikowe o średniej wysokości podnoszenia wideł (ok. 5,0m), z przemieszczaniem ze strefy przyjęć i piętrzeniem jednostek ładunkowych w strefie składowej na odległość do 170m. Stosowanie wózków podnośnikowych jest uzasadnione ekonomicznie tylko wtedy, gdy czas ruchu pionowego wynosi ok. 70% , a czas przemieszczania 30% całego cyklu pracy przy odległościach transportu 100 – 200m.
- Wózki ciągnikowe z przyczepami i naładowne przy dużych odległościach przemieszczania powyżej 170m. Wymagają one dodatkowych urządzeń załadunkowych i rozładunkowych na końcach odcinka przemieszczania.
Nośność lub udźwig środka transportowego.
Ze względu na manipulacje przeładunkowe istotna jest masa brutto jednostki ładunkowej, która powinna wynosić:
Qj < Qu
gdzie:
Qj – masa brutto jednostki ładunkowej,
Qu – nośność lub udźwig urządzenia przeładunkowego.
Wydajność pracy urządzenia przeładunkowego jest tym większa, im bardziej masa jednostki ładunkowej jest zbliżona do udźwigu lub nośności urządzenia.
Składowanie towarów
Składowanie towarów jest to zbiór czynności związanych z umieszczeniem (ułożeniem) zapasów na powierzchni lub przestrzeni składowej, w sposób usystematyzowany, odpowiednio do właściwości zapasów i istniejących warunków składowania.
Podstawowe zadania przy składowaniu.
Do głównych zadań fazy składowania należą przede wszystkim:
- przyjmowanie zapasów ze strefy przyjęć,
- kontrola profilu jednostek ładunkowych,
- przeprowadzenie korekty uformowania jednostek ładunkowych,
- przemieszczanie zapasów do czoła regałów lub stosów składowych,
- umieszczanie zapasów w urządzeniach do składowania lub stosach według ustalonej lokalizacji,
- przemieszczanie zapasów pomiędzy strefami składowymi,
- konserwacja zapasów,
- okresowa kontrola jakościowa zapasów,
- przemieszczanie zapasów z miejsc składowania do strefy kompletacji lub do strefy wydań.
Strefa składowa w pewnych warunkach może mieć zróżnicowane przeznaczenie, zależne od charakteru składowanych towarów (rezerwowe, bieżące). Charakterystyczną cechą tej sfery jest składowanie towarów w ustalonym miejscu oraz jednorodność postaci fizycznej od wejścia do wyjścia ze strefy.
Przy dokonywaniu doboru środków transportowych, które będą wykorzystywane w strefie składowej należy brać pod uwagę:
dostosowanie do specyfiki przedsiębiorstwa,
kompatybilność z posiadanymi urządzeniami,
wydajność umożliwiająca przyszły wzrost obrotów magazynowych,
możliwość rozwoju technicznego prowadzenia prac transportowo – magazynowych,
współdziałanie (synergię) poszczególnych operacji i czynności w przepływach towarów przez magazyn.
Metody lokalizacji towarów w strefie składowej
Ze względu na organizację pracy magazynu ważne jest rozmieszczenie towarów w strefie składowej. Odpowiednio do warunków pracy magazynu organizacja rozmieszczenia towarów wpływa na cykl realizacji operacji magazynowych, ich pracochłonność, wielkość potrzeb przestrzeni składowej oraz zarządzanie magazynem.
Wyróżnia się następujące podstawowe metody rozmieszczania asortymentów towarowych w strefie składowej:
- Rozmieszczenie według stałych miejsc składowych, polegające na przeznaczeniu dla poszczególnych grup towarowych stałych miejsc składowania (pól, sektorów składowych, gniazd w regałach). Metoda ta daje przejrzystość zagospodarowania przestrzeni, łatwość odszukania pożądanego asortymentu. W metodzie tej potrzebna jest duża przestrzeń składowa, równa maksymalnym zapasom każdego asortymentu.
- Rozmieszczenie według wolnych miejsc składowych, polegające na zagospodarowaniu przestrzeni składowej odpowiednio do wolnego miejsca w przestrzeni składowej, czyli tam, gdzie jest wolne miejsce. Zapasy są umieszczane w miejscach składowych wolnych w chwili dostawy. W metodzie tej potrzebna jest przestrzeń na poziomie średnich zapasów każdego asortymentu. Ponieważ częstotliwość przyjmowania i wydawania asortymentów towarowych jest zazwyczaj różna, dla składowanych zapasów jest potrzebna przestrzeń mniejsza o 20 – 25%. Metoda wymaga kontroli zarządzania przestrzenią składową za pomocą tablic dyspozytorskich a w dużych magazynach asortymentowych sterowania komputerowego.
- Rozmieszczenie według częstotliwości pobierania (rotacji), pozwalające wyodrębnić w strefie składowej sektory składowe zgodnie z kryteriami analizy ABC zapasów. Posiadając rozeznanie co do podziału asortymentów towarowych według kryteriów analizy ABC, należy je odnieść do maksymalnego skracania drogi przepływu towarów w magazynie. W układzie poziomym towary grupy A należy rozmieszczać w miejscach składowych w pobliżu najkrótszej odległości od drogi łączącej wejście i wyjście towarów w strefie składowej. W układzie pionowym asortymenty towarowe według kryteriów analizy ABC należy rozmieszczać:
w magazynach obsługiwanych układnicą lub wózkami wysokiego składowania, zgodnie z charakterystyką podnoszenia środków transportu (średnia wysokość podnoszenia),
w magazynach obsługiwanych ręcznie, zgodnie z zasadami ergonomii pracy rak człowieka.
- Inne metody rozmieszczania towarów w strefie składowej. W zależności od potrzeb stosuje się metody rozmieszczania według:
grup asortymentowych,
szybkości rotacji,
dostawców lub dostaw,
odbiorców lub odbiorów,
przynależności do określonego wyrobu (według kompletów),
zastosowanych pomocniczych urządzeń magazynowych.
Organizacja rozmieszczenia towarów charakteryzuje się tym, że są one umieszczane w przestrzeni składowej obok siebie według podanych kryteriów.
Istnieje możliwość realizacji różnorodnych kombinacji organizacji rozmieszczenia towarów w strefie składowej. Dobór metody jest uzależniony od wymagań, jakie muszą być spełnione względem składowanego zapasu oraz wynikają z funkcji i zadań magazynu w łańcuchu dostaw, przy czym bezwzględne jest przestrzeganie zasady FIFO wobec składowanych grup towarowych.